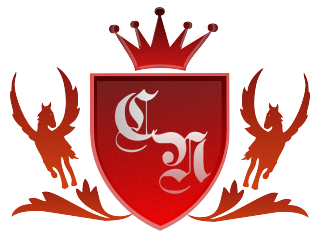
THREE-DIMENSIONAL MACHINING PROCESS DESIGN METHOD AND IT’S APPLICATION RESEARCH
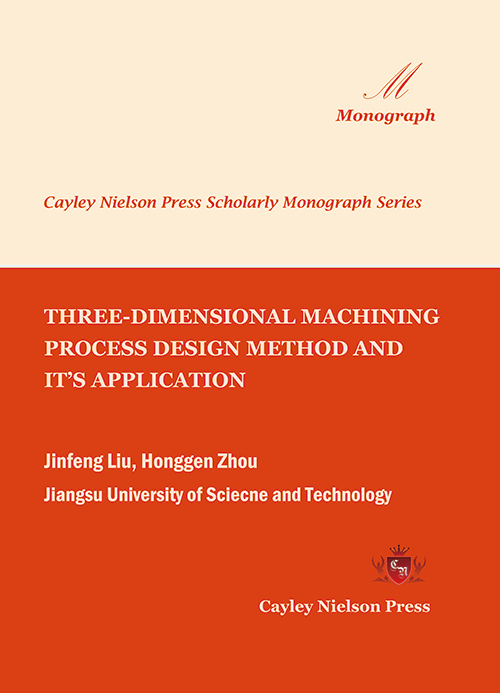
Jinfeng Liu, Honggen Zhou
Jiangsu University of Sciecne and Technology
Copyright © 2020 by Cayley Nielson Press, Inc.
ISBN: 978-1-7348822-1-6
Cayley Nielson Press Scholarly Monograph Series Book Code No.: 210-6-3
US$182.50
Preface
With the deep convergence of the new generation of information technology such as Internet of Things, cloud computing and big data, intelligent manufacturing has become the main direction of transformation and upgrading of manufacturing enterprises. Process design which serves as a bridge between product design and manufacturing processes has become a key link in the development of intelligent manufacturing mode. Taking the three-dimensional (3D) process model as the sole guide product processing has become the consensus among scholars, and the flexibility and intelligence of machining process design (MPD) has become the focus in the field of intelligent manufacturing.
The 3D-MPD is the core link of product design and manufacturing process, which has an important influence on shortening the product R&D cycle, improving product quality and reducing manufacturing cost. With the further application of Model Based Definition (MBD) technology, MBD model makes full use of the intuitiveness of three-dimensional modeling and the advantages of digitalization technology, and makes parallel manufacturing and information co-management possible while eliminating data inconsistencies, and MBD-based MPD has become a breakthrough in solving the effective organization and management of process. To this end, this book takes the creation method of MBD process models as the starting point, delves into the 3D-MPD theory and methods, and explores research methods such as MBD process models creation methods, process information reuse methods, the dynamic reconstruction methods.
The book's research is divided into five parts, the details are described below.
First part elaborates the content of 3D-MPD and overview its method. The first chapter mainly analyzes the present situation and existing problems of process design, and provides the basis for constructing the architecture of 3D-MPD method. The second chapter puts forward the key technology to be solved and the corresponding function decomposition, and constructs the architecture of 3D-MPD intelligent design system.
The second part elaborates the organization and management method of machining process and the creation method of the process models. The third chapter studies the acquisition, display, traceability, organization and management of process information by using MBD technology. Firstly, the characteristics of geometric information is accurately expressed by the MBD models, and the correlation mechanism between the process models and the process information is established; then the data objects of different process activities and their organization are studied; finally, the different granularity data organization based on the object-association method, process information hierarchy model and process information management mechanism are constructed. The fourth chapter studies the rapid creation method of machining process models based on feature recognition technology. Firstly, the processing features are classified and summarized based on the formation process and shape characteristics of the processing features. Then, the machining feature surface groups are taken as the research objects, its recognition algorithm is proposed based on the combination of process knowledge; finally, according the acquisition of the manufacturing feature and its creation order, the inter-process models are created by combining the manufacturing removal volume with the design model.
The third part explain the process information reuse method and the intelligent design method of machining process, which provides technical support for the rapid creation process planning. Fifth chapter studies the process information reuse method based on the matched similar machining features. Firstly, the integrated process route which realize the effective organization and expression of process information is established by the organization unit of machining features. Then an object-oriented method is used to create a multi-level manager to describe the processing feature information of each process, and the topology relation of the machining feature is expressed and recorded by using the adjacency matrix of the surface group attribute; finally, the process information is divided into process layer, feature layer and attribute layer, and the hierarchical retrieval method of machining features is put forward to realize the accurate matching of machining features. The sixth chapter studies the intelligence generation method of the machining process planning based on the process knowledge. Firstly, the process knowledge modeling and management method is proposed; then, combining the example reasoning and the rule reasoning, the process knowledge chain of the machining features and the skeleton process based on the series process knowledge chain are created; finally, the global optimal process route of the product is generated by genetic algorithm of the step information.
The fourth part explain the dynamic reconstruction method of the process plan. Seventh chapter study the maintaining method of process models and process information after design changes or process changes. Firstly, the specific form of process changes is elaborated. Based on whether the process models have changed after the process changes, the changes contents are divided into two types; then, the inter-relationships among the process models is constructed and the relationships are divided into independent and interdependent relations, and its correspond determination algorithm is proposed; finally, based on the relationship among process models, an algorithm of dynamic reconstruction of process models and automatic propagation method of process information are proposed.
The fifth part elaborates the 3D-MPD system and its functional application, this system provides a basic platform for the promotion and application of MPD. In eighth chapter, the 3D-MPD system based on modeling kernel or secondary development technology is developed. The system realizes the functions of 3D process planning models creation, process information management, process information reuse, process intelligent design. The application verification is carried out by the chosen some complex parts.
This research was funded by National Natural Science Foundation of China (51605204) and the China Postdoctoral Science Foundation Funded Project under Grant (2018M630536), in part by the Special Funding Project for Key Technologies of Ship Intelligence Manufacturing from the MIIT of China under Grant (MC-201704-Z02), and in part by the National Defense Basic Scientific Research Program under Grant (JCKY2018414C002, JCKY2018414C015). I would also like to extend thanks to authors contributing to the book chapters, especially the professor Zhong-Hua Ni and Xiao-Jun Liu of Southeast University, Li-Ping Cao and Feng Feng of Shanxi Diesel Engine Heavy Industry Co., Ltd, Hua Ye and Qun Li of the Hudong Heavy Machinery Co., Ltd and the graduate students Yu-ping Zhu, Peng Zhao, Ming-Ming Tang, Xu-Wu Cao, Su-Shan Sheng, Qiu-yan Cai. They offered help on sample characterization, data interpretation, and language improvement of the book chapters. At the same time, I would like to thank the authors who included the references in this book.
Jinfeng Liu, Honggen Zhou
Jiangsu University of Sciecne and Technology
May 20, 2020
Contents
Preface.....................................................................................................................................I
Chapter 1 Literature review.................................................................................................................1
1.1 The background and significance of the research.........................................................................................1
1.2 Review of key technologies for process design...........................................................................................2
1.2.1 Rapid creation of 3D process planning planning models.................................................................................2
1.2.2 Reuse process information based on matched machining features.........................................................................4
1.2.3 Rapid process planning based on process knowledge.....................................................................................6
1.3 Overview the proposed method............................................................................................................8
1.4 Summary.................................................................................................................................10
Chapter2 The mode of 3D machining process design driven by MBD process model................................................................12
2.1 Introduction............................................................................................................................12
2.2 Demand analysis of 3D machining process design..........................................................................................13
2.3 Structure and function analysis of 3D machining process design system...................................................................17
2.4 Architecture of 3D process design system based on MBD process model.....................................................................25
2.4.1 Frame of 3D process design system.....................................................................................................25
2.4.2 Business process model of 3D process design system....................................................................................26
2.5 Key technologies of 3D machining process design.........................................................................................28
2.5.1 Rapid creation of 3D process planning models..........................................................................................30
2.5.2 Process reuse technology based on the matched feature.................................................................................30
2.5.3 Rapidly generate technology of the 3D process planning based on the process knowledge.................................................32
2.5.4 Dynamic reconstruction technology of 3D process planning model........................................................................34
2.6 Summary of this chapter.................................................................................................................36
Chapter 3 Expression of 3D machining process models.........................................................................................37
3.1 Introduction............................................................................................................................37
3.2 Structure of 3D process planning model..................................................................................................39
3.2.1 Definition of 3D process planning model...............................................................................................40
3.2.2 Composition of 3D process planning model..............................................................................................42
3.3 Analysis and classification of process information......................................................................................43
3.3.1 Static process information............................................................................................................44
3.3.2 Dynamic process information...........................................................................................................46
3.4 Dynamic organization and management of process information..............................................................................48
3.4.1 Structural hierarchy of process information...........................................................................................49
3.4.2 Dynamic management of process information.............................................................................................52
3.5 Expression of 3D process planning model.................................................................................................56
3.6 Application analysis....................................................................................................................60
3.7 Summary.................................................................................................................................61
Chapter 4 The creation method of the 3D process planning models.............................................................................63
4.1 Introduction............................................................................................................................63
4.2 Overview methodology....................................................................................................................65
4.2.1 Related definitions of 3D process planning model......................................................................................65
4.2.2 Overview of 3D process planning model creation........................................................................................67
4.3 Management method of the machining features.............................................................................................68
4.4 Recognition algorithm of the machining features faces...................................................................................71
4.5 Mapping strategy between machining features and manufacturing feature volume............................................................80
4.5.1 Mapping algorithm for single volume machining feature.................................................................................81
4.5.2 Mapping algorithm for multi-volume machining feature..................................................................................83
4.6 Method for creating the 3D process planning models......................................................................................103
4.7 Case study..............................................................................................................................105
4.7.1 Machining feature mapping manufacturing feature volume................................................................................105
4.7.2 Create the 3D process planning model..................................................................................................109
4.8 Summary.................................................................................................................................110
Chapter 5 Process reuse method based on the matched machining features......................................................................111
5.1 Introduction............................................................................................................................111
5.2 Basic concepts..........................................................................................................................114
5.2.1 Machining feature faces...............................................................................................................114
5.2.2 Main machining face...................................................................................................................115
5.2.3 The expression model of integrated process information................................................................................116
5.3 Overview methodology....................................................................................................................118
5.4 Hierarchical organization of process information........................................................................................120
5.5 Description of machining characteristics................................................................................................122
5.6 Hierarchical retrieval of machining features............................................................................................124
5.7 Case study..............................................................................................................................126
5.8 Summary.................................................................................................................................130
Chapter 6 Intelligent generation technology of 3D process planning based on process knowledge...............................................132
6.1 Introduction............................................................................................................................132
6.2 Existing problems and method overview...................................................................................................134
6.3 Basic concepts and overview of the approach.............................................................................................136
6.3.1 Basic concepts........................................................................................................................136
6.3.2 Overview of the approach..............................................................................................................141
6.4 Modeling and management of machining process knowledge..................................................................................144
6.4.1 Modeling of machining process knowledge...............................................................................................144
6.4.2 Management of machining process knowledge.............................................................................................146
6.4.3 Creation of process knowledge base....................................................................................................150
6.5 Generation of skeleton process based on process knowledge...............................................................................151
6.5.1 Combination of identical relationship machining features..............................................................................152
6.5.2 Accurate process information acquisition based on rules and cases.....................................................................153
6.6 Generation and optimization of accurate process.........................................................................................158
6.6.1 Relationships between machining features and process constraints......................................................................159
6.6.2 Workingsteps sequence matrix..........................................................................................................163
6.6.3 Process constraint matrix based on geometric reasoning................................................................................165
6.6.4 Intelligent optimization sequencing of working steps..................................................................................167
6.7 Intelligent generation of machining process based on process knowledge..................................................................173
6.8 Conclusions.............................................................................................................................176
Chapter 7 Dynamic reconstruction technology of process model................................................................................178
7.1 Introduction............................................................................................................................178
7.2. Literature review......................................................................................................................180
7.3 Process changes contents................................................................................................................184
7.4 Working procedure model's interrelationship and its judgment method.....................................................................187
7.4.1 Interrelationship between process models..............................................................................................187
7.4.2 Method of judging the working procedure model relationship............................................................................189
7.5 Dynamic reconstruction algorithm of working procedure model.............................................................................193
7.5.1 Dynamic reconstruction algorithm for process sequence adjustment......................................................................193
7.5.2 Dynamic reconstruction algorithm after process model editing..........................................................................199
7.6 Automatic dissemination of process attribution information..............................................................................203
7.6.1 Automatic dissemination of annotation information.....................................................................................203
7.6.2 Automatic dissemination of general attribution information............................................................................207
7.7 Summary.................................................................................................................................209
Chapter 8 3D process deign system development and application...............................................................................210
8.1 Introduction............................................................................................................................210
8.2 Design and development scheme of 3D machining process design system.....................................................................211
8.2.1 Prototype System......................................................................................................................211
8.2.2 System architecture...................................................................................................................213
8.3 Introduction to system modules..........................................................................................................215
8.3.1 Functional structure design of prototype system.......................................................................................215
8.3.2 System interface diagram..............................................................................................................216
8.4 Cases study.............................................................................................................................218
8.4.1 Organization and management of process information....................................................................................218
8.4.2 Creation of process models............................................................................................................220
8.4.2.1 Design model of bracket parts.......................................................................................................220
8.4.2.2 Module for creating 3D process planning models......................................................................................221
8.4.3 Dynamic reconfiguration of process model..............................................................................................226
8.4.4 Output of process files and browsing of lightweight process models....................................................................229
8.5 Summary.................................................................................................................................230
References..................................................................................................................................232
Readership
This book should be useful for students, scientists, engineers and professionals working in the areas of optoelectronic packaging, photonic devices, semiconductor technology, materials science, polymer science, electrical and electronics engineering. This book could be used for one semester course on adhesives for photonics packaging designed for both undergraduate and graduate engineering students.